What Is Pick And Pack & Why Is It Important?
Last updated: June 2024
Getting your warehouse’s pick and pack process right can make or break your operations.
Get it right, and you'll fulfill orders faster and more accurately than ever before.
Get it wrong, and your entire operation can fall into chaos.
That’s why we've created this comprehensive guide covering everything you need to know about warehouse order picking systems and how using an inventory management software like Veeqo, along with a high-quality scanner, can enhance your picking and packing process.
What is picking and packing?
Picking and packing is the system where you take your customers’ orders and place them into a shipping box.
This system eliminates the need for repacking during shipping, cutting down on the time it takes to fulfill each order.
Due to its speed and simplicity, it’s the preferred system for most e-commerce retailers who deliver small orders.
Businesses that fulfill larger orders may take the goods to a designated location in the warehouse and then pack them using the appropriate packaging and materials.
Why having a good pick and packing process important
A good picking and packing process improves the speed and accuracy of your warehouse operations.
This results in fewer mispicks, fewer returns, and more happy customers who receive what they want when they expect it. In fact, over one in ten one-star reviews complain of a mispicked item.
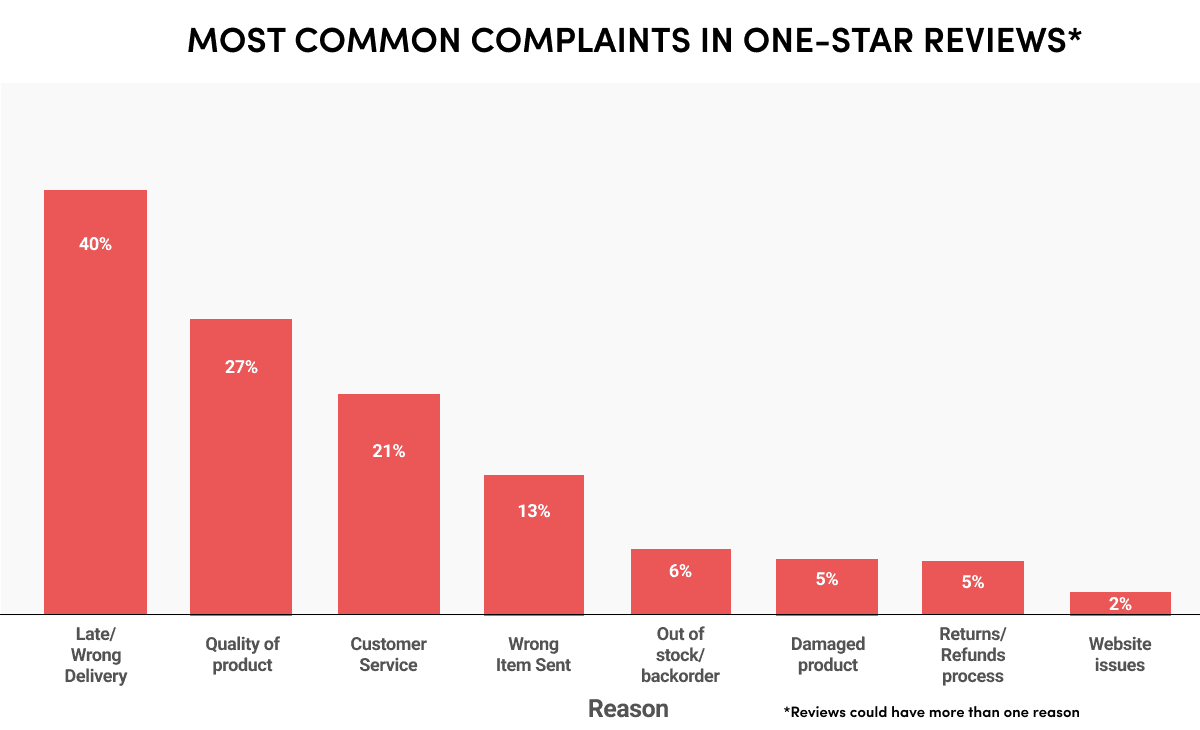
A good pick and packing process is also an efficiency saver. Research for our picking & packing ebook revealed that 70% of labor time when processing customer orders is taken up by just picking the products.
What is the pick and pack process?
The pack and pick process has four key steps:
1. The order is received
Assuming you have ecommerce fulfillment software, once an order has been placed on one of your ecommerce channels a packing slip will be generated.
With Veeqo, this packing slip will give the picker the optimal order to pick the items in.
2. Picking
The warehouse worker, or picker, retrieves the items from the warehouse shelves as listed on the packing slip. The efficiency of this stage directly impacts overall business efficiency and profitability.
3. Packing
Picked items are compiled and placed into a designated bag or box along with any necessary dunnage or promotional materials. A printed shipping label is then affixed.
If you use a shipping software like Veeqo to buy and print your labels, you can batch print up to 100 labels and packing slips in just two clicks. One of Veeqo's sellers, Mike Truffa who owns beauty retailer, A1 Great Deals, said recently that this feature saves him 6-hours of time per day. This allows him to use that time on other business tasks.
After printing the label, Quality Assurance checks are performed to ensure order accuracy and appropriateness of packaging before the packages are ready for shipping.
What is Quality Assurance? Quality Assurance measures come into play to ensure that there is no mismatch between what your customer ordered and what was picked by the associates. These checks include packaging appropriateness, labeling accuracy and order accuracy. After QA is done, the finished packages are ready for shipping.
Shipping
The packages are then arranged by your team for the shipping carriers to deliver.
How to improve Picking Accuracy
Before we can discuss specific order picking systems, let’s quickly discuss a few general ways of improving accuracy and warehouse productivity within order picking, irrespective of the warehouse management system you use:
1. Dedicate a bin location to each SKU
Clearly label areas, rows, shelves, and sub-locations in your warehouse.
Avoid mixing multiple SKUs in the same bin to prevent confusion and mispicks. Dedicated bin locations enable pickers to quickly and accurately locate items.
Further reading: How to Design Your Warehouse Layout for Maximum Efficiency

That’s why you never want to mix multiple SKUs in the same bin or sub-location. Visualize a picker going to a bin location and manually deciphering between two colors, or different sizes or any other minor variation. It’s going to be a huge waste of time because your pickers will inevitably pick the wrong items, especially during busy periods.
On the other hand, when SKU has a dedicated bin location, pickers can head straight there and pick the right item in their first attempt.
2. Minimise walking time
Our internal research shows that pickers spend 60% of their time walking around the warehouse between picks. Reduce this by:
Batch picking multiple products.
Organizing picks for efficient routing (Veeqo helps with this).
Creating clear pathways and directions.
Investing in a quality warehouse management software can do all this on your behalf, freeing up even more time and energy to focus on other warehouse tasks. Alternatively, there are also powerful (and free!) warehouse management softwares!
3. Arrange your warehouse based on sales figures
Most retailers generate 60% of their sales from just 20% of their product catalog. Meaning there’s usually a sub-set of products that create the bulk of a business’s orders.
This means that certain products are likely to be picked more often than others. Therefore, it makes perfect sense to store these as close to the packing station or desk as possible.
You can use ABC Analysis to categorize inventory by sales and then arrange your warehouse accordingly. It’s a great way to determine which items might need prioritizing over others:
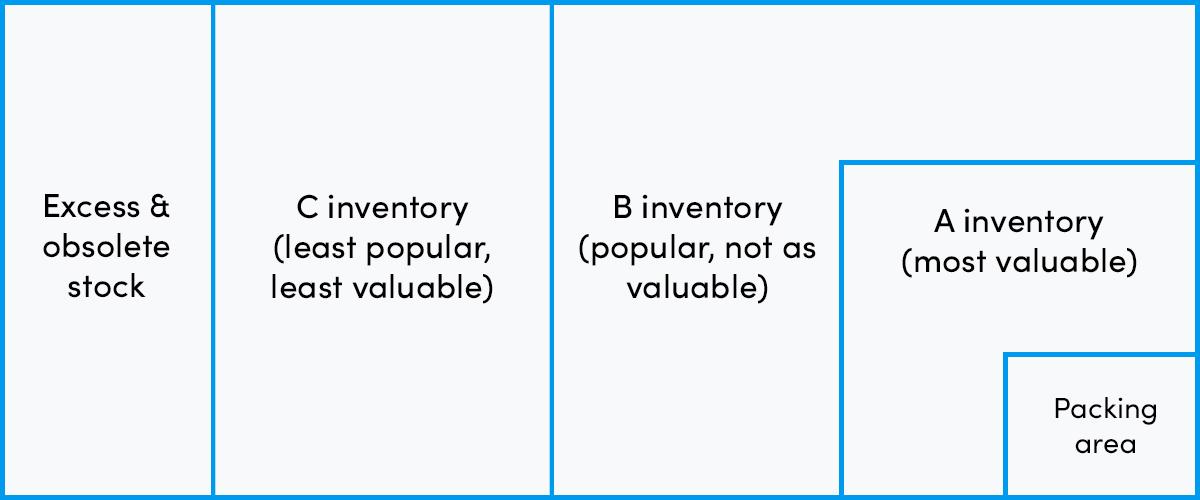
It may even help to store the best-selling items within the shelves above the packing desk/stations itself to make for super-simple access.
Warehouse order picking systems
Picking the right warehouse order picking systems entirely depends on your distinct business needs. With that said, retail warehouses typically use four main packing methods:
1. Single order picking
The most basic and ‘barebones’ picking process – typically useful for businesses that are just starting out. It is based on a fairly straightforward premise:
A picker picks one order at a time throughout the entire cycle before moving on to the next.
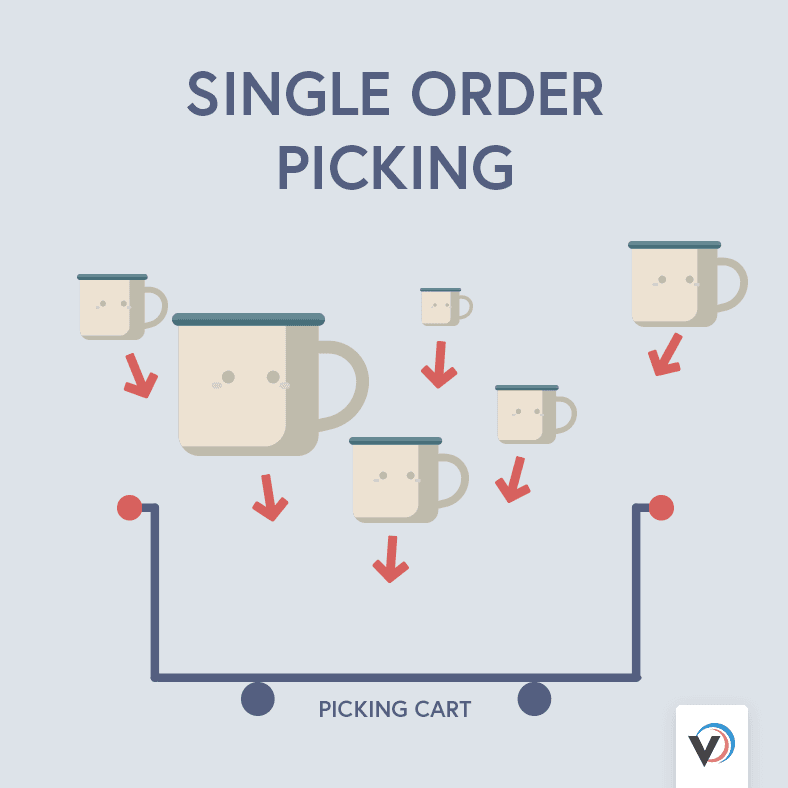
This picking and packing method is best for retailers who are just starting out and haven’t seen the kind of growth and expansion to gain any real benefits from using more complex methods.
Single order packing should be avoided if you’re shipping more than 20 customer orders per day or plan to anytime soon.
2. Batch picking
This method is practically as simple as the first one, yet offers better efficiency as long as you comply with the general warehouse picking productivity guidelines discussed above this section.
It works along the following premise:
Each picker is assigned to a batch which contains multiple orders.
The picker moves into the warehouse and picks all the orders in one sweep.
All the items are returned to the packing desk.
A new batch is received and the process starts over.
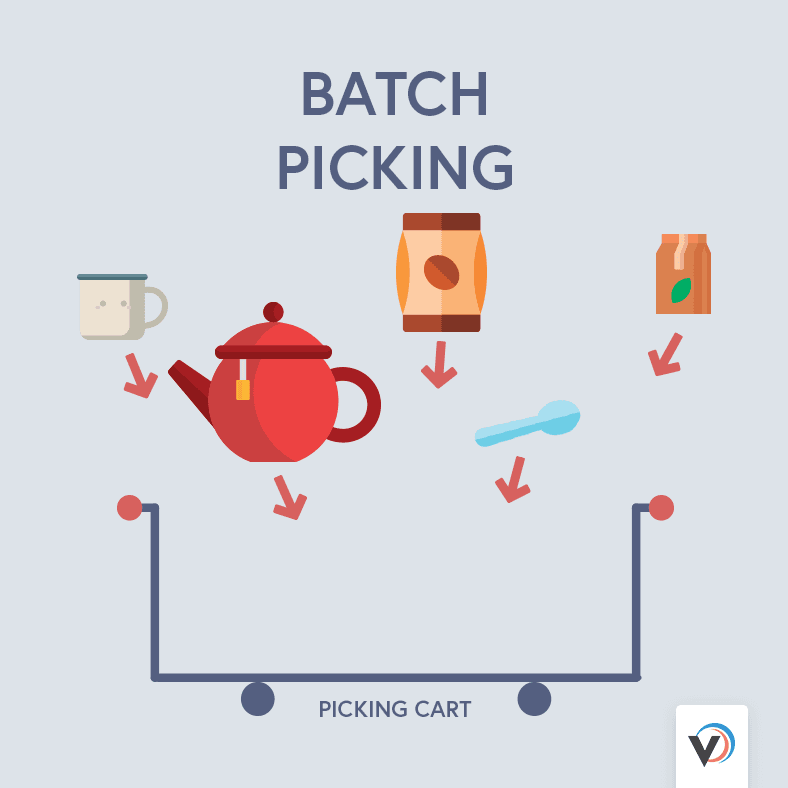
The number of orders per batch is typically between 10 and 30. However, this depends on the physical dimensions of the products and average order size. Therefore, it pays to allocate batch sizes based on the total number of items and not the total number of orders.
This method is ideal for a high volume of orders where there is a single product or a generally low number of products per order.
Batch picking should be avoided if there is a high volume of products per order or you’re planning to pick and pack a high volume in the near future.
3. Zone picking
Zone picking is where order picking systems tend to get somewhat advanced. Under this scenario:
Each picker is assigned their own ‘zone’ or area within the warehouse.
They can only pick products stored in the assigned zone.
Each order is passed through all the zones/areas to have any required items added to it by the respective picker in that zone.
Once the order has passed through all warehouse picking zones, it is passed on to the packing desk to be completed.
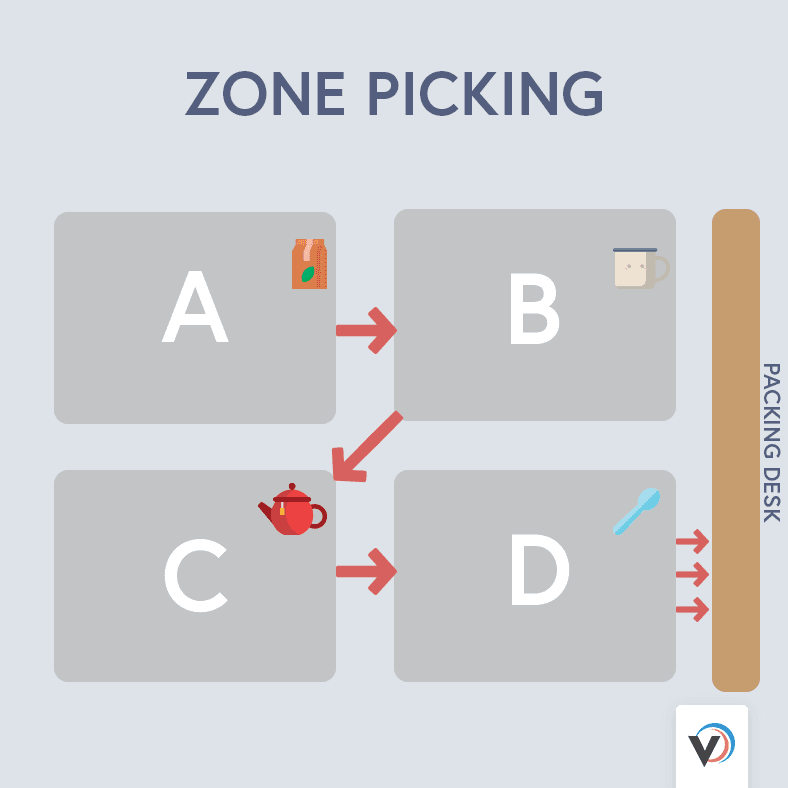
This picking method is perfect for preventing multiple order pickers getting in each other’s way when high-volume orders are being dealt with. However, it can create a slight shipping delay because each order must pass through all the respective zones before getting shipped.
Therefore, it’s best for retailers who ship a high volume or multiple-item orders each day.
It’s not ideal for shipping single-item or low-volume orders, or where there are a limited amount of pickers.
4. Wave picking
Wave picking is similar to zone picking – with the only exception being that all zones are picked at the same time and not sequentially. Here’s what happens:
Just like the previous picking method, all pickers get a designated warehouse zone to pick from.
Each order picker picks the relevant items in an order within their zone.
The picker returns to a central packing station or desk.
A dedicated packer then consolidates each pick into a single order.

Wave picking offers the same benefits as zone picking where high volumes of multiple-item orders must be dealt with – but without the shipping delays. However, labor costs can increase because the packer may need to spend more time combining picks into a single order before they can be shipped off.
Wave picking is best for retailers shipping a high volume of multiple-item orders each day, who also prefer super-fast processing and shipping.
It isn’t ideal for single-item or low volume orders, or where the desired number of pickers are not available, or cost-cutting is more important than dispatching and shipping timelines.
Automated warehouse picking systems
Thanks to the pace at which technology has evolved, we now a number of fantastic options for automated warehouse picking:
1. Pick to light system
This system involves a barcode scanner and light setup. The order picker scans a barcode and is then guided to the appropriate warehouse area through LED lights, which can be integrated on the floor, ceiling or along other equipment where orders are picked and packed.
So, essentially, all a picker has to do is scan a barcode and follow the lights:
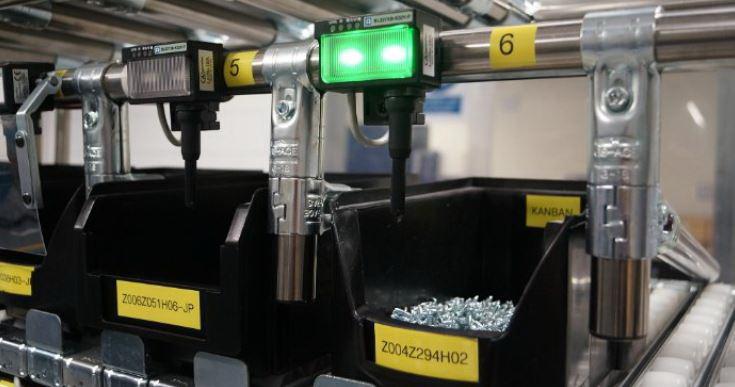
One downside, however, is that this method can get overwhelming fairly quickly for larger operations where high-volume orders with expansive product catalogues must be processed.
2. Voice picking system
Voice technology has found its way into warehouse picking too and much to everyone’s delight!
Pickers wear a headset to receive instructions on what to pick and where to go, after which they verbally relay the confirmation of a pick to the picking system via the attached microphone. A very useful system indeed as it leaves pickers with free hands to dedicate towards the actual picking, and there’s also no paperwork to deal with once picks are completed.
3. Mobile scanner picking
Equip your warehouse and inventory with unique barcodes and have your pickers pick using a quality mobile scanner. This allows your pickers to:
Have a list of orders which can be picked exclusively by each picker.
Have an optimised walking route to pick all orders, saving time and resources.
Scan and confirm picks with almost perfect picking accuracy.
Perform much quicker picks on average.
That’s not all – the scanner can also be used to confirm overall accuracy during the picking process and other warehouse management tasks as well.
How to measure order picking success
After choosing the appropriate order picking system, you must track or measure how well it is performing. We need to take two elements into consideration: accuracy and speed, and, in that very same order.
There’s not much point in making super-quick picks if your customers get incorrect items or partially complete orders. So, here are the main warehouse picking KPIs you must track:
1. Rate of return
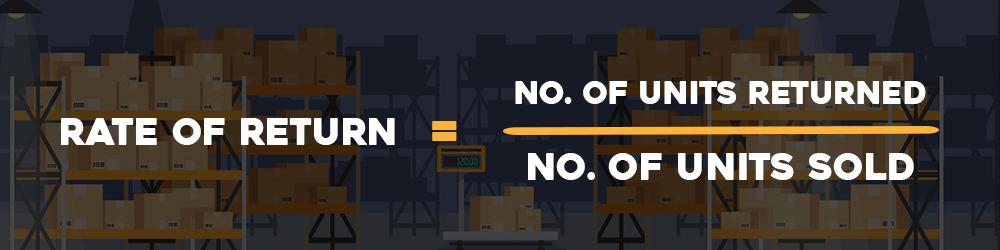
At a glance, this simply refers to how often items are being returned by customers but we need to determine the ‘why’.
There a many factors responsible for returned orders – something which is not under your order pickers’ control. This is why we’re going to segment this KPI into different reasons for a return. This way, anything returned as a result of incorrect or missing items (only) would squarely be the responsibility of your order pickers.
So, come up with different reasons for products being returned and then use this equation to analyze each one: Rate of return = Number of units returned/number of units sold.
2. Picking accuracy
The next step is to use your segmented ‘rate of return’ data, which you acquired using the above formula, to come up with a specific KPI for picking accuracy.
Take your total number of orders for a specific time period and the number of incorrect items returned within the same period, and apply them to this equation:
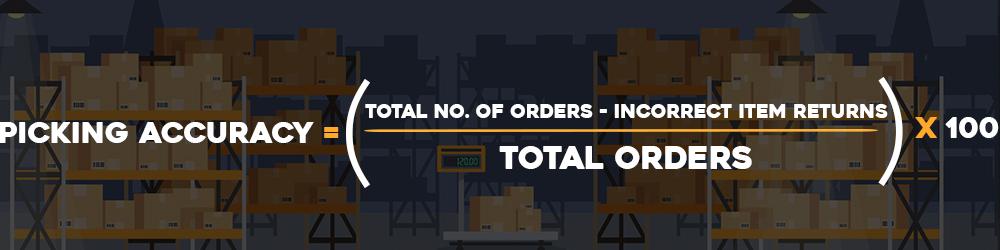
3. Average order processing time
Naturally, order processing time does not come down to pickers only. There’s a lot more happening ‘under the hood’ than just picking, when it comes to order processing speed and accuracy.
But let’s revisit our earlier statistic: 70% of labor time when processing orders is consumed in picking alone. So:
Average order processing time should roughly indicate how quickly your pickers are operating, right? Therefore, tracking this on a month-to-month basis can prove to be a key insight. Here’s what you need to do:
Record the time it takes from start to finish for each order processing
Divide by the total number of orders processed for that time
Veeqo can record everything for you and displays it on an intuitive Dashboard for easy access:

In Summary
The more your business scales, the more complex order picking can potentially become. So it’s absolutely essential to get this process down as perfectly as possible. In fact, customer satisfaction, business reviews and sentiments, and especially your corporate image, rely on this.
While choosing any one of these order picking systems according to your requirements is vital, combining it with some kind of barcoded automated system is how you’re going to reach next-level order picking, and even reach a new level of eCommerce fulfillment as well.
About the author
This article was written by Marc Girdlestone. Marc is Product Manager at Veeqo. His particular focus is all things warehouse-related, making sure Veeqo offers the functionality its users need to make a success of their ecommerce businesses.