The Complete Guide to Warehouse Management Systems
Good warehouse management is key to the success of any ambitious ecommerce retailer. To get it right you need to understand both how to organize your warehouse and when, and how, to implement a warehouse management system (WMS).
Doing this can seem daunting, that’s why we put together this guide to cover every aspect of warehouse management and warehouse management systems.
An efficient warehouse can be key to the foundation on which your business grows. An inefficient one can throttle any chance you have of success.
What is warehouse management?
Warehouse management is the act of organising and controlling everything within your warehouse – and making sure it all runs in the most optimal way possible.
This includes:
Arranging the warehouse and its inventory.
Having and maintaining the appropriate equipment.
Managing new stock coming into the facility.
Picking, packing and shipping orders.
Tracking and improving overall warehouse performance.
Most high-growth retailers would use automation tools (like some form of warehouse management system) to control this part of their supply chain. However, there are many aspects that can and need to be considered from a manual standpoint. And so we cover this entirely in this guide.
Warehouse management statistics
The UPS Pulse of the Online Shopper 2017 reports that 44% of consumers say speed of delivery is a reason they choose to shop at marketplaces over other online stores.
And Volume Five of that same report claims that 63% say delivery speed is important when searching for and selecting products, with 77% willing to pay for expedited shipping.
Temando’s 2017 State of Shipping in Commerce Report claims that 54% of UK shoppers would buy from a competitor when the delivery service they seek isn’t provided – 10% more than US buyers.
54% of customers under 25 said same-day shipping is their number one purchase driver.
33% of customers said they value speed more than any other factor when choosing products. Second only to cost.
13% of all bad reviews on Trust Pilot relate to the wrong item being sent out.
45% of 5-star trust pilot reviews give fast shipping as a reason.
How to arrange your warehouse
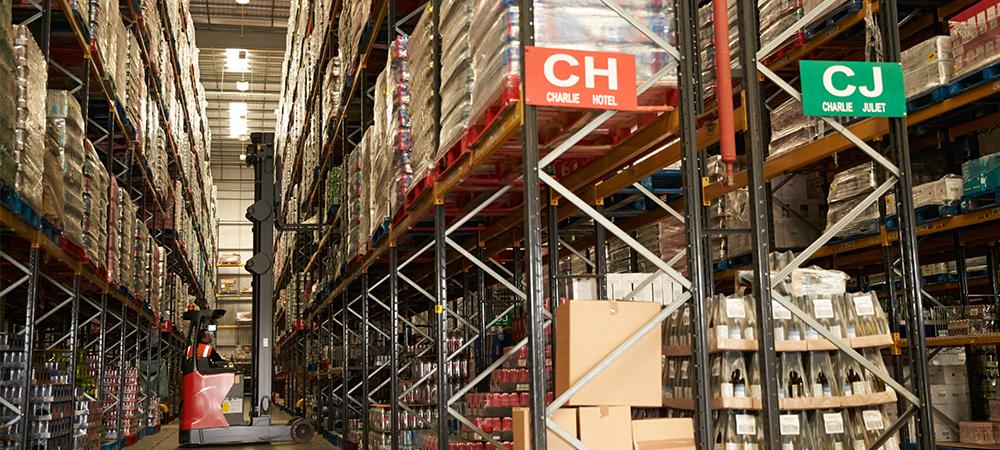
Probably the most important first step in optimizing your warehouse operations is making sure you have everything in there arranged in the most efficient way.
Here’s what you need to think about:
1) General warehouse layout
Planning the layout of your warehouse is centered on balancing two things:
Providing enough storage space for your inventory;
While still having enough working space for staff to move around and complete their tasks.
And this generally requires (although it depends on individual business requirements) having a space designed to house the following areas:
Receiving new stock area.
Unpacking and booking in new stock area.
A warehouse office.
Main storage area.
Excess, obsolete or dead stock storing area.
Packing area.
Shipping station.
This can be tricky – especially when dealing with limited space. So it’s best to sketch out your warehouse layout to scale before setting it up or changing what you already have.
Using a grid system makes planning this a lot easier:

Space and maneuverability is a key thing to remember. Pickers need to be able to walk up and down aisles without getting in each other’s way. And should also have enough room to actually pick items.
2) Labelling areas of your warehouse
Effective warehouse management can’t be done without set location names for stock that have been clearly labeled.
Your team should be able to look at your warehouse system and see exactly where any product is located.
Practicality is king here. Sticking with simple alphanumeric combinations makes it easier to understand and decipher for pickers trying to reach that site location.
For example, you can start by simply including labels for specific rows, shelves, and then exact bin locations:

So you always know, for example, that all your blue t-shirts sized medium will be in Row A – Shelf B – Bin 1. And the pattern can be continued like this.
Bigger warehouses with more rows may need to add a little more detail:

And then even larger warehouses may even need to be split up into different areas for each row and the facility as a whole:
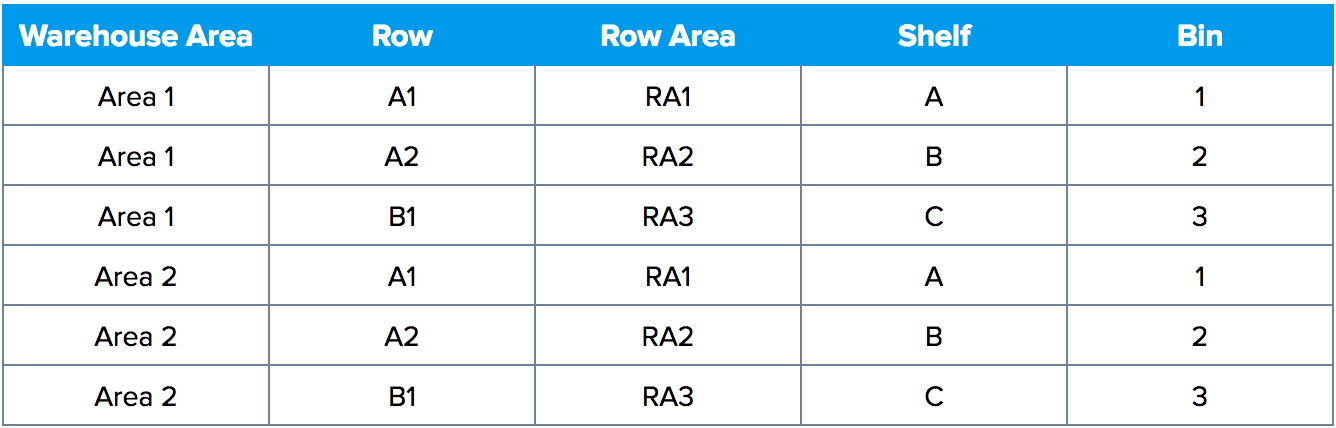
How detailed you go with labeling depends totally on the size of your facility or site, the complexity of your warehouse operations and a range of other factors.
But in short:
The bigger your facility, the more in-depth you’ll need to go with your location labeling to achieve optimal warehouse management.
3) How to arrange inventory in the warehouse
So at this point, we have a warehouse that’s laid out and labeled in the most optimal way for your business. But this now raises the question:
How do you determine the exact location each product should be stored?
The answer:
Keep better selling products closer to the packing desk.
Research we conducted on over 20 Veeqo retailers found that 60% of a company’s sales tend to come from just 20% of their products. Meaning you can severely reduce picker walking time by:
Identifying that 20% of products from past sales data in your business;
and then storing these as close to the packing desk as possible.
Tools like ABC Analysis tend to be used more in inventory management. But this can provide some handy information when it comes to this part of warehouse management too.
Divide all on-hand inventory into three groups – A, B and C:
A Items: Are of high value and bring in most of profits.
B Items: Are sold often, but less valuable/profitable than A items.
C Items: The rest of your inventory that doesn’t sell much and generates the least revenue.
You can then decide that ‘A items’ will be placed closest to the packing desk, while ‘C items’ will be farthest away. Like this:
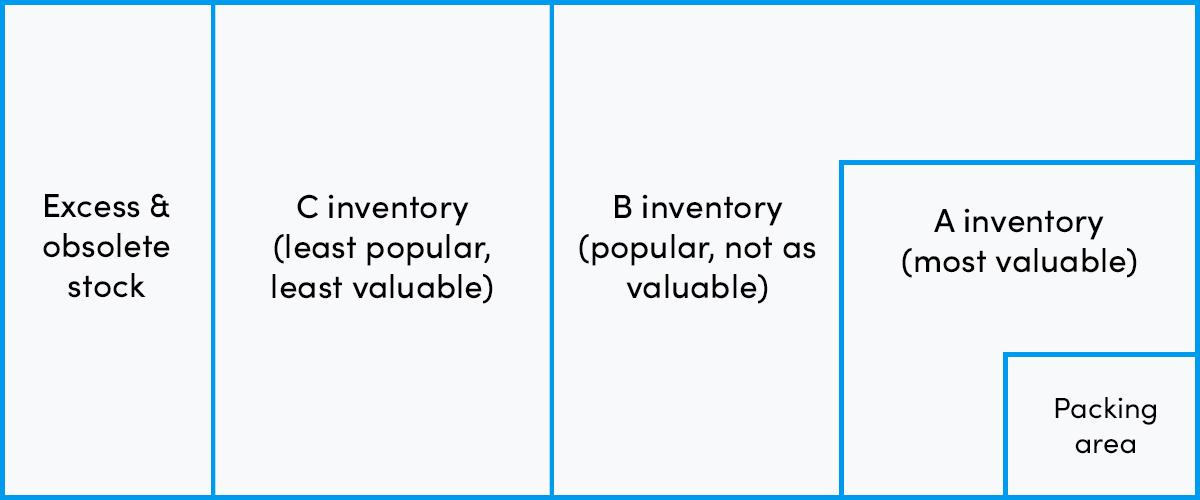
Some small and lightweight items may even be sold frequently enough to warrant being stored on shelves above the packing desks themselves.
This means packers can quickly add these into relevant orders and pickers can focus on bigger items.
Finally:
You can take this concept another layer deep by also identifying which products are most commonly sold together.
So faster selling products are stored closer to the packing desk and products commonly purchased together are stored close or next to each other. Meaning you’re doubling down on reducing walking time for each picker.
4) Don’t be afraid to rearrange
A small final point in this warehouse management section is this:
Don’t be afraid to rearrange your warehouse.
Yes – it can take time and resources to implement and may seem like more hassle than it’s worth. But an optimally arranged warehouse can save bags of time overall and severely reduce costs for the entirety of your supply chain management.
While inefficiencies can seriously hamper growth. So regularly evaluate and – if necessary – rearrange or upgrade.
For example:
It may be that your best-selling products in summer become your worst selling come winter, and vice versa. Or you sell more of specific products on key retail dates through the year. Or you’ve switched some products to prestige pricing that might not sell quite as frequently.
So it makes sense to rearrange these products in line with this when the time comes – moving some closer to the packing desks and others farther away.
5) Warehouse equipment
A successful warehouse operation means having the best equipment in your warehouse too.
Make sure to think about the following:
Warehouse equipment list
Shelving units. The most common ones have metal frames with wooden shelves, are easy to build, yet robust. Access to both sides can also be very useful – one side for putting in, one for taking out.
Bins. Each bin will be labelled and assigned to a specific variant to make it easy to locate in the warehouse.
Picking carts. Pickers will need a cart on which to carry all the items that are being picked before returning to the packing station – especially for
Totes. Usually simple plastic containers that sit on the picking cart, and will only ever hold items for one order at a time
Packing desk. Solid, larger than a normal office desk and has rolls so that you can get easy access to your packaging materials.
Packaging materials. Your different sized shipping boxes, tape and all the protective inner packaging – like bubble wrap, shredded paper or air pillows.
Printers. Good quality A4 laser printer for invoices, and a typical 6×4” shipping label printer (
is great for this). For your A4 printer, think about speed of printing the first page, speed of printing multiple pages and cost per page.
Shipping computer. Dedicated computer (ideally touchscreen) solely for shipping out orders – printing labels, marking orders as shipped, sending out tracking details and/or using shipping software.
Shipping scales. These weigh all packed shipments and send details to your shipping computer via a direct connection.
Dymo are, again, a great option for scales.
CCTV. Inventory is a business asset, and should be protected from shrinkage – CCTV is a great option to deter theft.
Receiving and managing new stock
Stock doesn’t just appear out of nowhere. And so a critical part of warehouse management is being able to receive, unpack, put away and book in new inventory as efficiently as possible.
The faster this happens, the sooner that stock becomes available for sale.
And what’s more:
Any errors or inefficiencies in this process will then cascade through the entire supply chain.
Here’s what you need to consider:
Have appropriate space. There needs to be enough space in your receiving area to both temporarily house newly delivered stock without risk of damage and for your team to perform the necessary tasks with it.
Have assigned workers. New stock needs to be dealt with as soon as possible – not left to build up. Make sure it’s clearly communicated whose job it is to do this.
Record everything. It’s a good idea to record relevant details to fall back on if there are any problems – e.g. exact timestamps of when new stock arrives and is put away.
Inspect carefully. Dedicate some time and resources to ensuring all new deliveries are correct in number and free of damage. This is a great opportunity to identify any vendor, inbound shipping or packaging problems.
Put away. Add any necessary labelling or barcodes before physically putting the stock away to be stored in its relevant warehouse place.
Update inventory. Make sure all the stock levels are correctly updated on each sales channel or inventory management system – meaning it’s live and ready for purchase.
There are three simple options for how this can be done:
1) Receiving via paper
Receiving your new stock via paper isn’t the most optimal way. It leaves you open to errors and huge time lags between when stock is delivered and when it becomes ready for sale.
But it is still doable – especially if you deal with very low volumes of product and orders.
Simply run through the paper PO, count delivered to inventory, and tick off the stock as correct quantities are verified.
You’ll need to make a note of any errors and follow up with the supplier manually.
2) Receiving via automated system
A much better option is to use management software to receive and update new inventory.
For this, we’ll dive into Veeqo’s Purchase Orders tool:
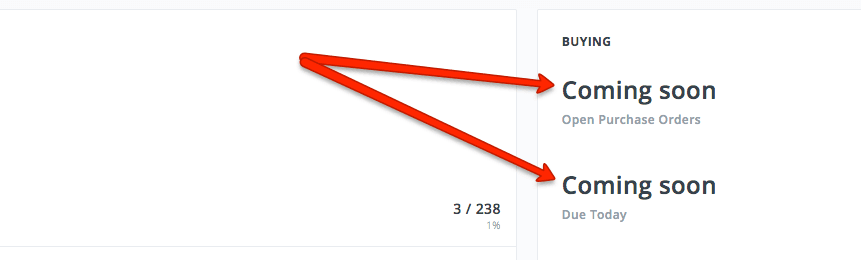
You’ll be taken to a list of all active purchase orders.
When a PO is delivered to your warehouse, simply open it up in Veeqo to receive items into inventory.
If all delivered items are correct in quantity, just select all items and click Receive:
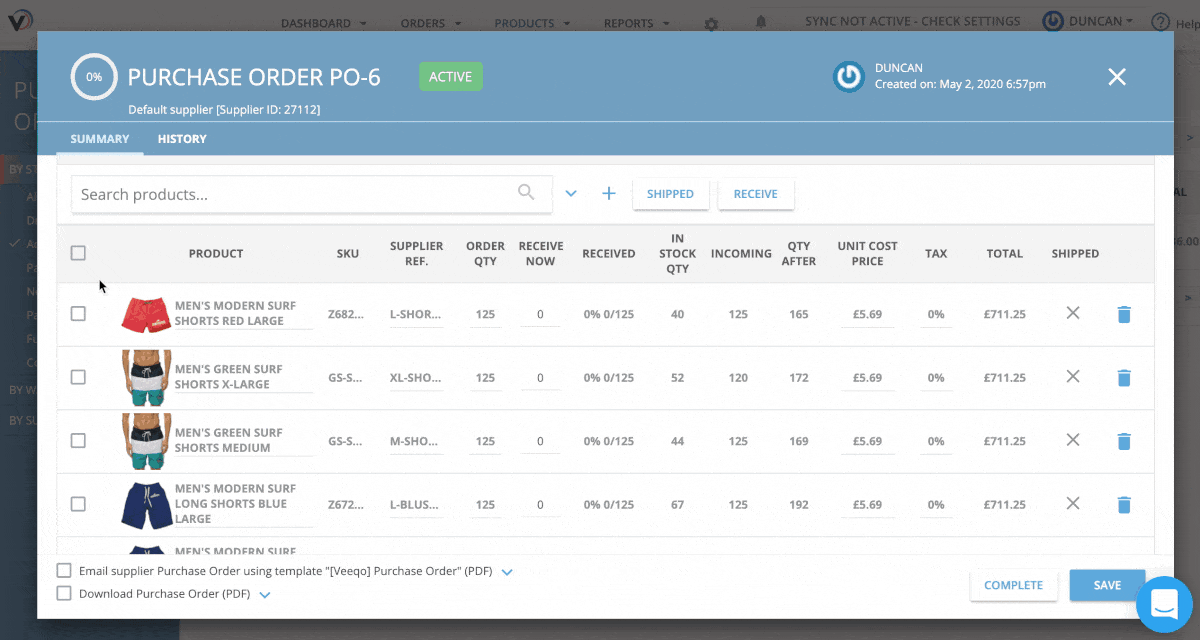
If delivered item quantities are different from what was expected, just make an edit in the “Receive Now” box and click Save:
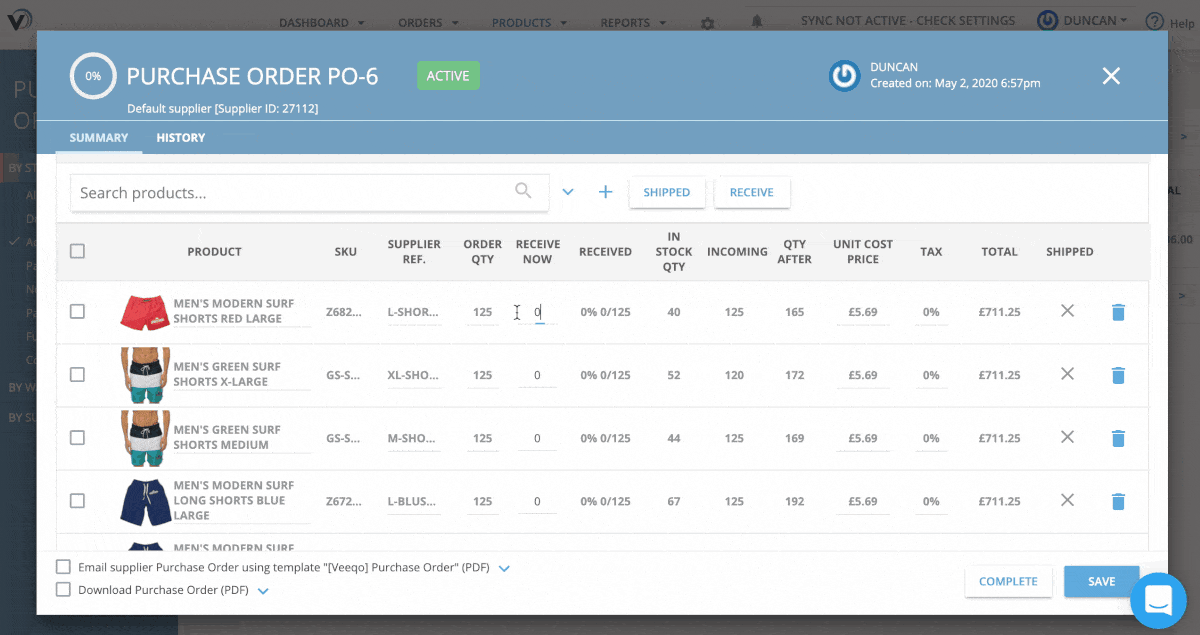
The stock will then be instantly either:
Assigned to any open back orders.
Added to available inventory, and reflected across relevant sales channels and warehouses.
A mobile barcode scanner device can make this whole booking in process even quicker and more accurate.
Rather than sitting at a desktop computer, you’d simply:
Scan a product or purchase order, or search for it on your device.
Update inventory levels on the mobile screen – making the inventory available for sale.
And put it away in the warehouse.
So you basically go through the same process as mentioned in the previous point, but in the palm of your hand:
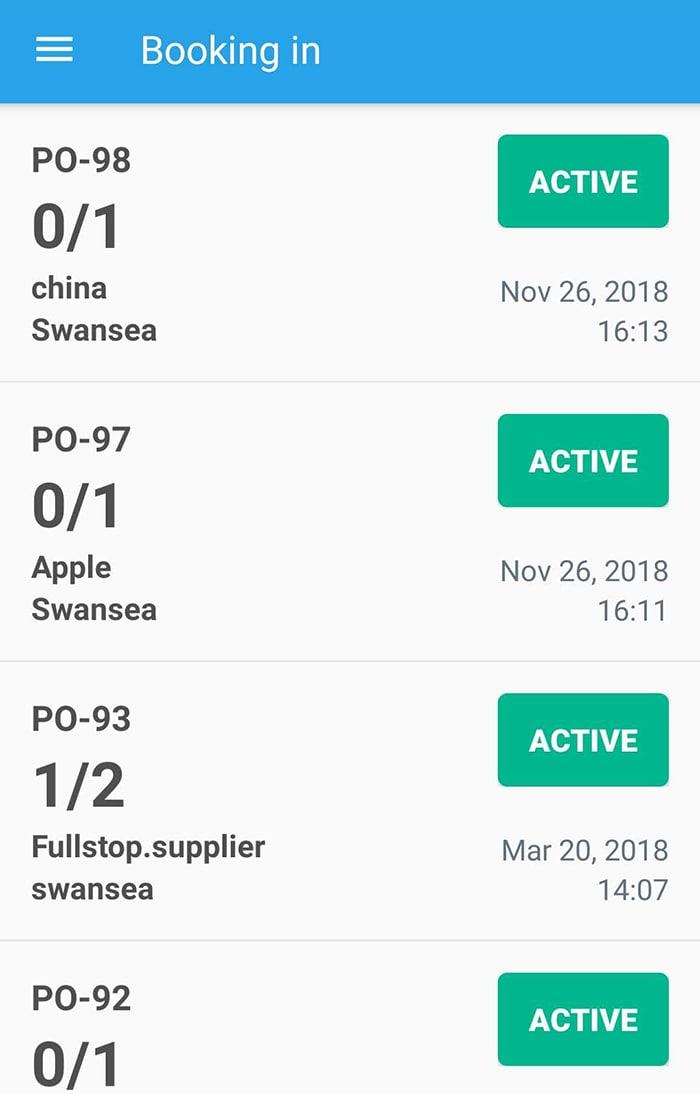
Making it a much easier and quicker process.
Warehouse management fulfilment strategies
Being able to fulfill orders quickly and accurately is an absolute staple of good warehouse management.
After all, it’s pretty much the entire reason for the warehouse existing in the first place.
Here’s what you need to think about when it comes to picking, packing, shipping, and your distribution strategy in general:
1) Choosing an optimal picking system
Picking may seem like a simple concept at first. And it is – when you only have a few orders to deal with.
But this becomes a much different story once you’re dealing with hundreds (or even thousands) of multiple item orders each day.
In fact:
Research we recently conducted on 20 Veeqo retailers found that 70% of labor time when processing order is spent on just picking the products. And 60% of a picker’s time is taken up by simply walking around the warehouse.
So getting a solid picking system in place can have a major impact on overall distribution productivity.
These are the four main picking systems or methods used by medium to large retailers:
Single order
This is the most basic picking method – typically only used by those just starting out. Quite simply, a picker will pick one order at a time in its entirety before moving on to the next.
Best for: Retailers just starting out who aren’t yet big enough to gain the benefits of more complex picking methods.
Avoid if: You ship more than 20 customer orders a day (or plan to in the near future).
Batch picking
The picker is assigned a batch consisting of a number of orders, picks them all in one go, and then returns to a packing desk. The picker will then get assigned a new batch to pick.
The number of orders allocated to each batch is generally between 10 and 30. But this really depends on the physical size of your products and the average order size.
Best for: High number of orders with a single or low number of products per order.
Avoid if: You have a high number of products per order (or are aiming for this in the near future).
Zone picking
This sees each picker assigned their own area (or zone) of the warehouse with them only picking products stored in that specific zone. An order is passed through all areas to have any required items added to it by pickers in that zone before being returned to a packing desk.
Great for preventing multiple pickers from getting in each other’s way, but it can also create a slight delay in shipping as each order needs to be passed around the warehouse.
Best for: Retailers typically shipping a high volume of multiple item orders.
Avoid if: You typically ship single or low item orders or have very few pickers.
Wave picking
Similar to zone, but all zones pick at the same time. The various items are picked in the according to zone and are then given to a packer who will consolidate all the separate picks for each order.
This is faster than zone, but labor costs increase due to the packer needing to spend more time combining orders at the end before needing to be shipped.
Best for: Retailers typically shipping a high volume of multiple item orders and still want to maintain a super-fast process.
Avoid if: You typically ship single or low item orders, have very few pickers or cost is more important than speed of dispatch.
Here’s a quick summary of all four methods:

2) Optimising your packing process
There’s more to packing than just throwing items in a box as quickly as possible.
It’s an opportunity to make completely sure that you’re sending the right products to the right customers and in the most efficient way.
Here’s what you need to consider:
Box size
More and more shipping companies are incorporating package dimensions into their pricing – rather than it being based solely on weight.
Meaning box sizes could be having a direct impact on costs.
However:
Having 50 different box size options is a great way to overwhelm packers and severely slow down warehouse operations. So there’s a balance that needs to be struck here.
Of course, it depends on your individual business needs.
If you know every order is the same physical size then having one box size makes sense – and it’s a lot easier for the packer.
But a typical retailer will usually do best with around 3-5 size options. This keeps things manageable for packers while still allowing room to minimize courier costs.
Packaging material
Another element to the packing process is choosing the most appropriate packaging material.
This is all about striking a balance between:
Keeping the goods protected during transit.
Minimising the overall weight of the package (and therefore courier costs).
Keeping the cost of the packaging material itself down.
Obviously:
Shipping a Fabergé egg is going to warrant a better (and more expensive) packaging material than if shipping a book.
So it’s worth analyzing your product catalog (and track record of delivering damaged items) to determine the range of packaging materials you need to have available.
Here are some of the most common ones:
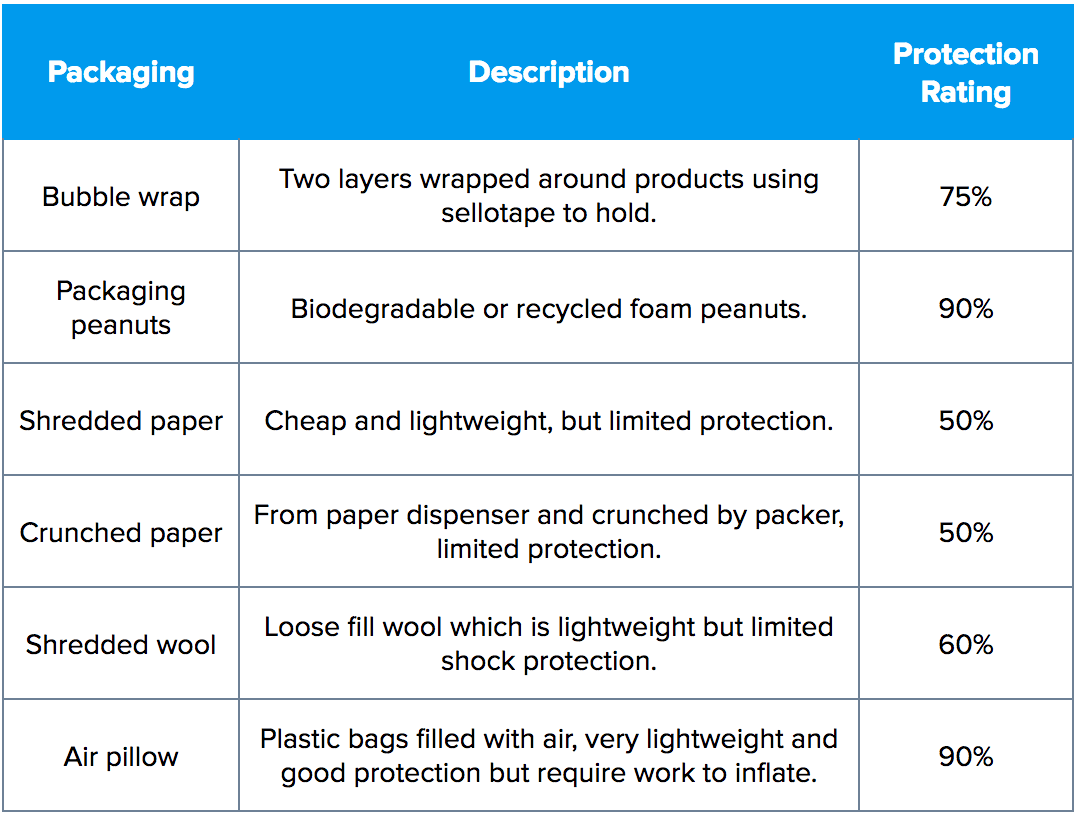
3) Shipping your orders
The next few steps in your warehouse management process are pretty straightforward:
Weigh the package.
Print out relevant shipping label (and invoice, if not already done so). SEE ALSO: V-Print: The Quick New Way to Print Labels & Invoices in Veeqo
Mark the order as ‘Shipped’ on the relevant sales channel or Order Management System.
Send out ‘shipping confirmation’ and ‘tracking’ emails to the customer (a quality Order Management System will do this for you automatically).
SEE ALSO: How to Skyrocket Customer Retention with a Perfect Order Management Process
Measuring warehouse performance

Tracking performance and working to improve it is essential when it comes to all parts of supply chain management.
And it’s no different when it comes to warehouse management.
In general, this is all about two things:
Accuracy of fulfilling customer orders (without damage).
Speed of fulfilling customer orders (without damage).
With this in mind, here are the main KPIs you want to be tracking to specifically measure the success of your warehouse management process:
SEE ALSO: 7 Essential Warehouse KPIs to Set Your Operations Manager
1) Receiving efficiency
This is quite simply how long it takes for your team to complete the receiving and putting away of a newly delivered purchase order.
It’s a good idea to record exact timestamps for:
New stock being delivered.
When this stock is ready for putting away.
Then again once the stock has actually been put away.
You can then calculate the difference in time between each point and work out an average for the month – allowing you to see how performance is trending in this area of your warehouse operations.
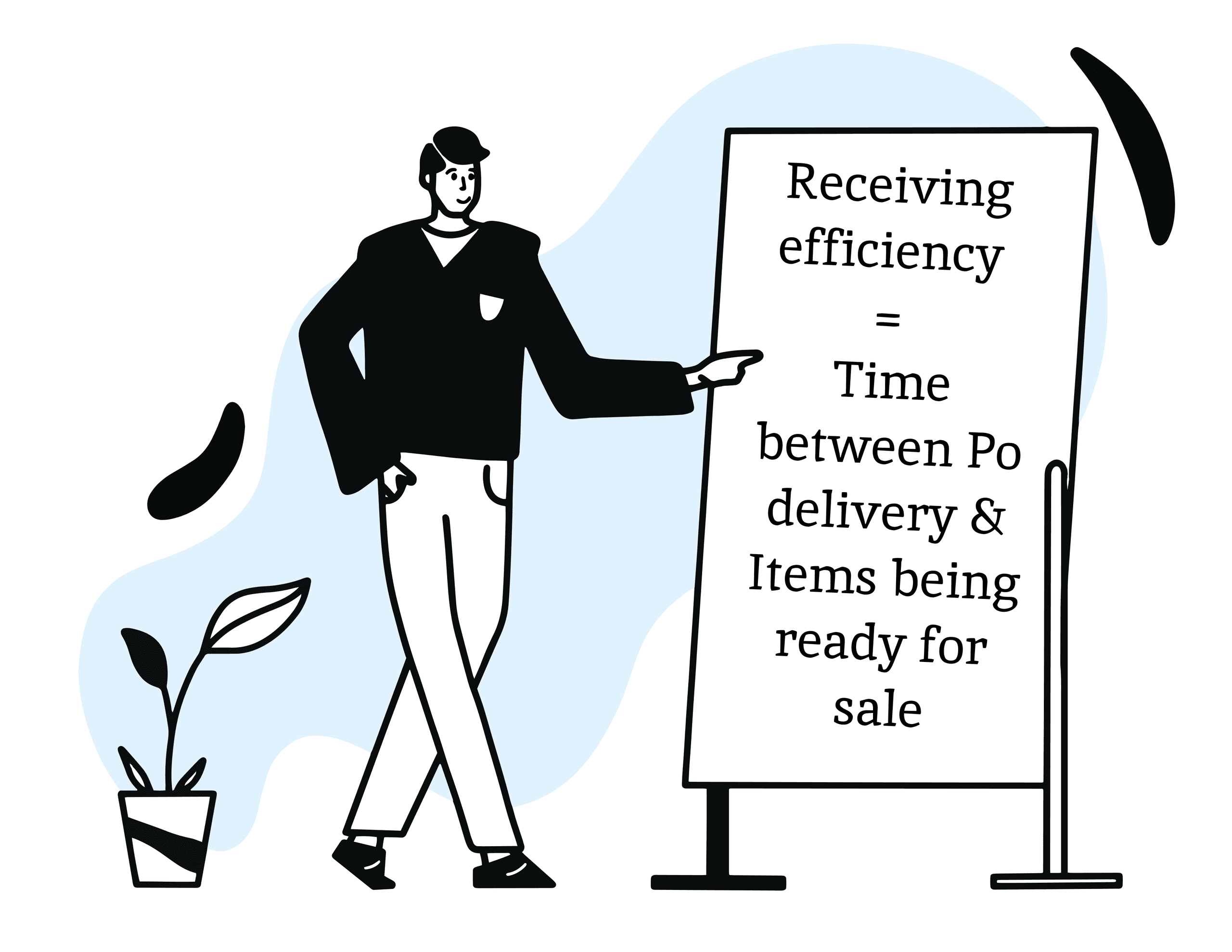
2) Rate of return
An order being returned isn’t always down to a problem in the warehouse – a customer may have just had buyer’s remorse.
So the key to getting the best use out of this is to segment by reason for return. This way, the warehouse or operations manager can start looking at exact reasons why this KPI may be high and put into place strategies to resolve it.
Determine several different return reasons and use the following equation to analyze each one:
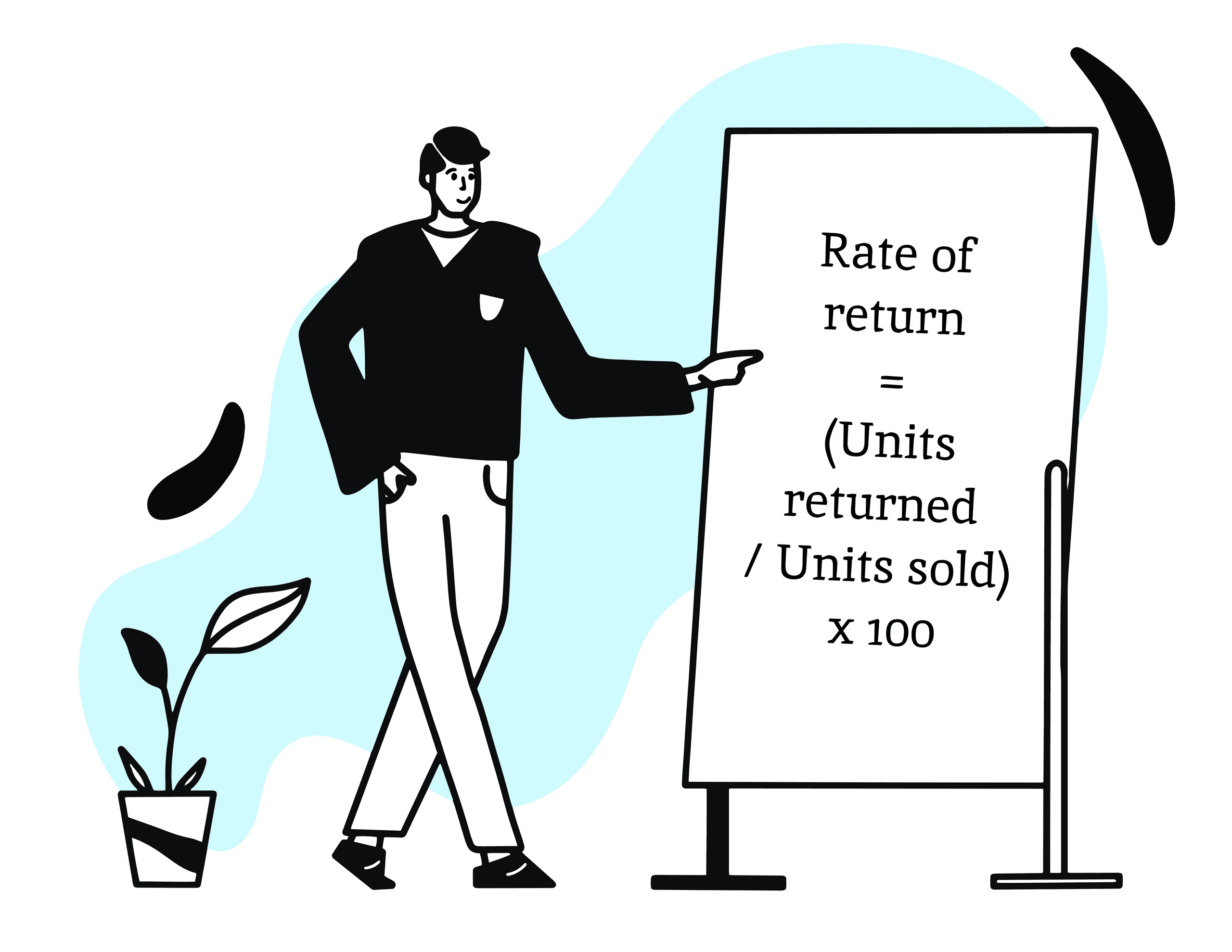
3) Picking accuracy
Tracking and segmenting rate of return properly lets you also analyse picking accuracy – a particularly key piece of data.
To calculate picking accuracy, use your total number of orders in a period along with data from the rate of return KPI in the following equation:
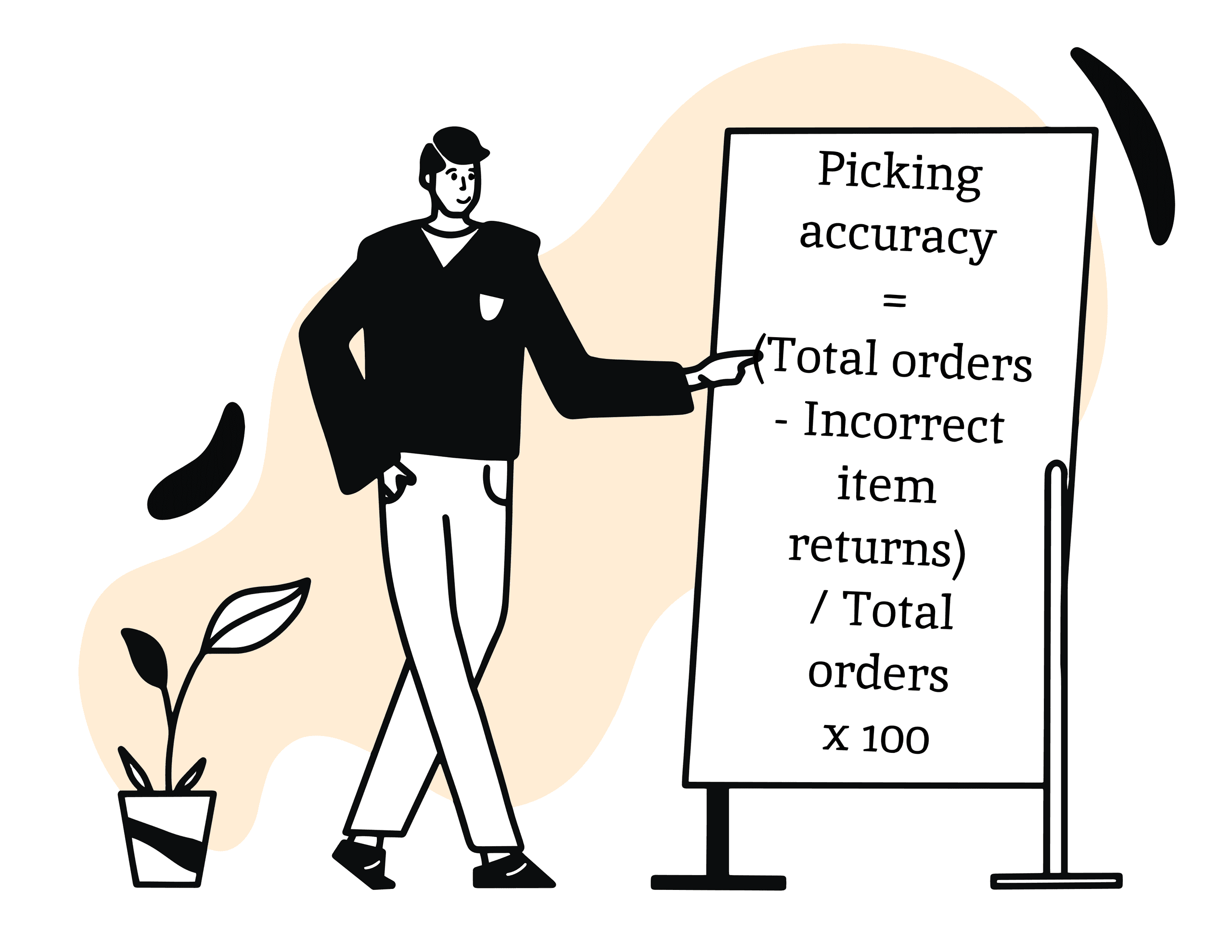
4) Order lead time
Order lead time (or average order processing time) is quite simply how long it takes for a customer to receive an order.
You may want to divide this into various categories. For example, international orders, Amazon Prime orders or orders for special or larger products.
But generally:
The lower you can get order lead time, the happier your customers are going to be – so long as it arrives in perfect condition.
What is a warehouse management system (WMS)?
A warehouse management system (WMS for short) lets organizations control, manage and administer warehouse operations. Giving complete visibility of warehouse operations from when goods enter the warehouse to when they are shipped out.
How do warehouse management systems work?
Warehouse management systems work by keeping track of all products and warehouse operations. They sync up your warehouse operations with your inventory management and order fulfillment processes. Allowing ecommerce businesses to easily keep on top of their warehouse operation.
There are two main types of warehouse management system you can choose: standalone and integrated.
Choosing a Warehouse Management System
Warehouse Management Systems or Warehouse Management Software of some kind can basically take a huge chunk of the leg work out of all the above processes.
They’ll automate and digitize as much as possible. Making it much easier to:
Keep everything organised, tracked and documented.
Pick with as close to perfect accuracy as possible.
Speed up your entire logistics operation.
But it can be tough sifting through all the information to decipher when to upgrade and what to actually look for in your management software.
When to upgrade to a Warehouse Management System
As with many things, it’s totally dependent on your individual business needs if/when you’re ready to upgrade Warehouse Management Systems.
Questions to help decide when to upgrade Warehouse Management System:
Is your current process achieving a 99.9% picking accuracy rate? If not, how costly is each incorrectly picked order to the business?
What are your other warehouse KPIs looking like? And how beneficial would improving each one be?
How many team members is it taking to run your current operation?
And would it be more economical to replace some with a Warehouse Management System or piece of software?
How many orders are you dealing with each day? And how much annual turnover is this generating?
Have you been achieving growth targets? And how quickly do you plan to grow in the short to medium future?
Which one is better for you: a standalone or integrated warehouse management system?
If you use a standalone you will need to integrate it with the rest of your operational systems. While an integrated solution will encompass your whole order management process.
Before choosing the best one for your business, you should consider the advantages and disadvantages of both.
Standalone WMS
A standalone WMS is a warehouse management solution that focuses just on warehouse management. While it may integrate with other solutions its features will be warehouse focussed.
Advantages
Offer a wide array of warehouse operations features: such as cycle inventory counting, warehouse reports and different picking options.
Should be capable of integrating with operational solutions, such as; inventory management software, point of sale cysts, ERP solutions etc.
Disadvantages
Lack of visibility over processes. As they are only concerned with warehouse operations, there may be gaps in your reporting when trying to look at the entire fulfillment process.
Standalone solutions can be time-consuming as you have to log in to different products to complete the ecommerce fulfillment process.
Often these are not suitable for multichannel ecommerce as they will not include real-time integration with sales channels, nor will they often provide complete inventory tracking and control features. Making it harder to keep on top of your stock levels.
They can be cost-inefficient as you will have to purchase other solutions to be able to manage your fulfillment.
Integrated WMS
This type of wms will have the same database as the rest of your order management system. Meaning that your entire order management flow will be integrated together.
Advantages
Integrated systems give you one centralised system for your order fulfillment needs. This means your orders, inventory and shipping information are perfectly in sync at all times.
Advanced reporting and forecasting.
As this type of system keeps track of all your order fulfillment data, it can be used to create more comprehensive reports and make more accurate forecasts.
Saves time and money.
As you only have one software to login and use this reduces the time it takes to manage your fulfilment process. It also makes it easier for your staff, as they only have to learn how to use one system. You also only have to work with one support team and only have to pay for one solution.
Disadvantages
Depending on the standalone and the integrated solution you are choosing from, it may be that the integrated one has fewer warehouse, or less specialized, functions.
Ten steps to choosing a warehouse management system
Choosing the right warehouse management system can often be as simple as taking a few considerations into account:
Step 1. Understand your current systems
If you are already using software to manage your warehouse operations or part of your warehouse operations, then you should start by looking at it in detail. What functions does it have that you like? What functions does it not have that you want?
You will also need to know what integrations you require from your warehouse management system. For example, you may require it to integrate it with your shipping carriers or sales channels.
Step 2. Decide if your picking process requires a WMS
If you are running a very small ecommerce operation, like a side-hustle, a WMS is unlikely to be necessary. But, if you are moving any reasonable number of products or you have any ambitions to scale you will need a more sophisticated solution.
Step 3. Understand what you are looking for in a warehouse management system
This is where you make your checklist of ‘must-haves and ‘like-to-haves’. You can then compare this list against your options.
Step 4. Decide on your budget
Of course, good warehouse management systems will cost money. So you will need to know how much money you can commit from your cash flow to purchasing one.
Step 5. Create a shortlist
There will be a few different options you can choose from. The easiest way to decide which ones to shortlist is simply to create a list or spreadsheet listing prices and features.
Obviously, we hope you choose Veeqo! But the key is making the right choice for your business.
Once you have created a shortlist you can then go and use free trials or book demos with those you think are right for you.
Step 6. Check it integrates with your entire fulfillment process
Warehouse management is only part of the puzzle of ecommerce. Your WMS should also connect with your inventory management system and shipping carriers.
Veeqo is a complete ecommerce fulfillment platform, so it covers all of these areas in one platform. But not every WMS does.
Step 7. Check it gives you the reports your need
A good warehouse management system will give you reports that can make definite improvements to your business. It should provide these reports in an easily accessible way.
It’s also good if the WMS provides demand forecasting as this will help prevent under and overstocking in the future.
Step 8. Check it works with your ecommerce tech-stack
You probably use a range of platforms, marketplaces, sales channels and shipping carriers. You need to check that your warehouse management system either has a native integration, seamless workaround or open API to do this.
This is where you can make use of a free trial. As it’s hard to know if a system works for you without testing it out.
Step 9. Is it easy for pickers to use and understand?
A good WMS will be easy for your pickers and warehouse team to understand and use. While there will always be a training period with any new software, you should look for an intuitive interface and easy-to-understand processes. This will make it easier for your team to pick up the new system and cut down on training time for new hires.
Step 10. Does it come with support?
Your business will be unique, therefore it’s important that any service you purchase comes with support. This support will be able to help you through any issues that arise with the product.
Key features of warehouse management systems
There are many different warehouse management solutions on the market, so choosing one that suits your business needs can be daunting. So, here are some of the key features you should look for in your warehouse management system.
Automation
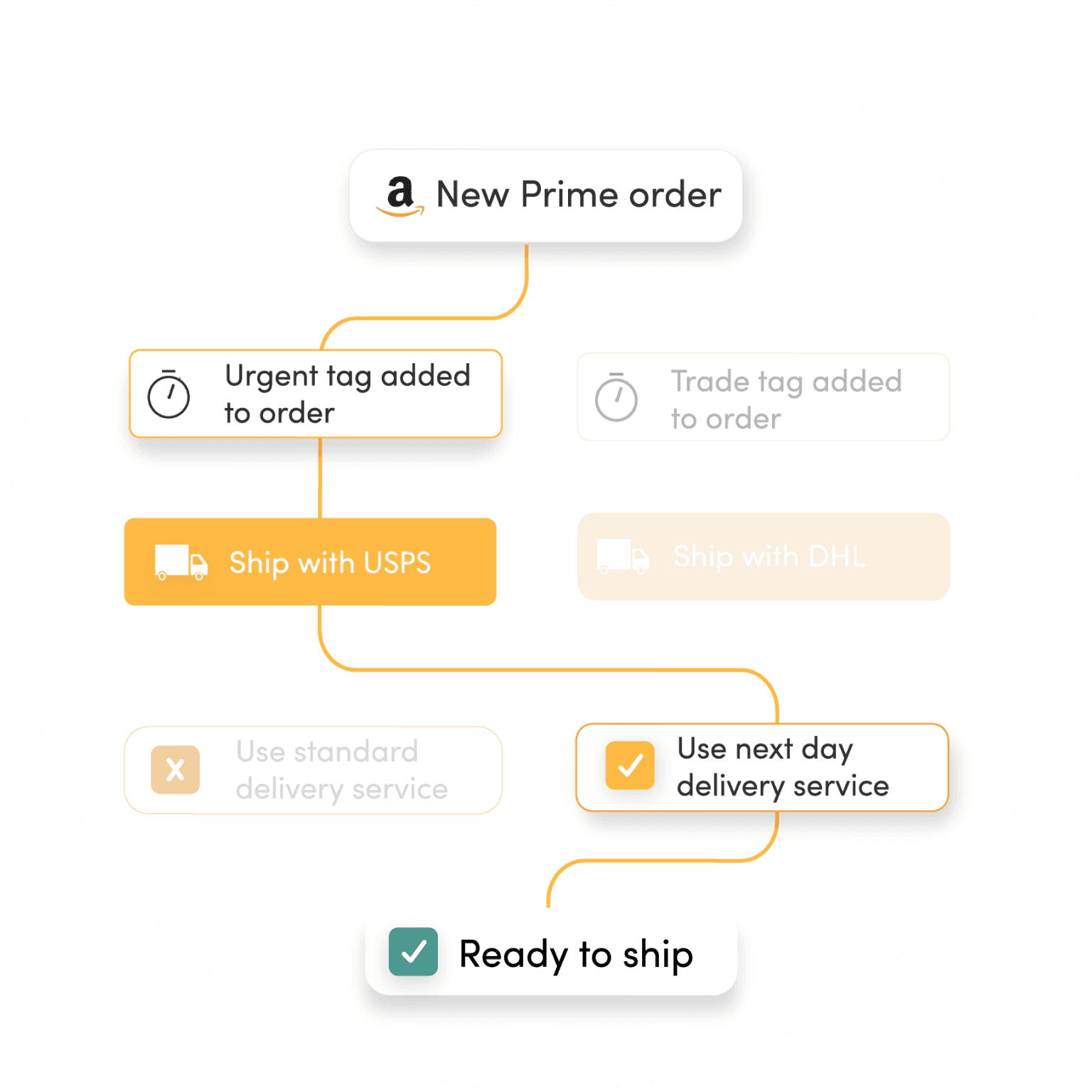
Automation can be a great tool for an ecommerce business to save time and be more efficient. Automation should be able to help you reduce the scope for human error in your fulfillment process. This is because, once set up, what happens to products is determined based on pre-set rules. Which your picking and packing team then just needs to execute.
Digital picking
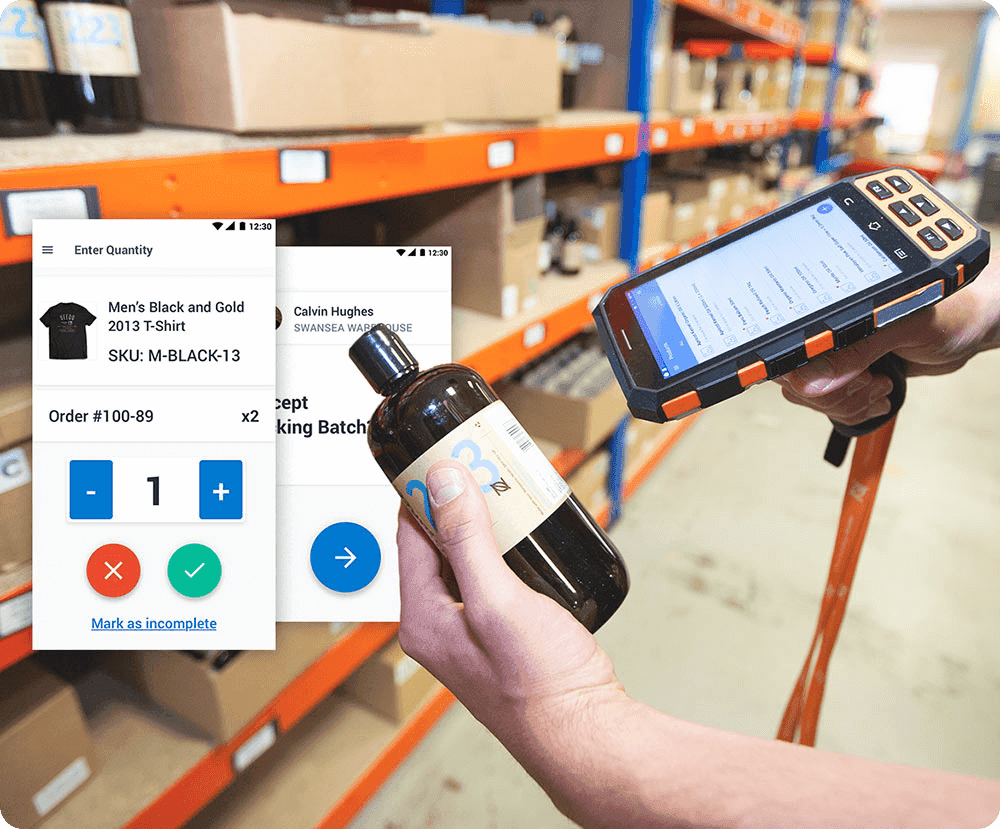
While many ecommerce businesses start out with paper picking, as they grow they will probably want to move towards digital picking. Whatever warehouse management system you choose, it should be set up to allow for digital picking if it is going to be in any way futureproof.
Easily accessible reports
Ecommerce is a data-driven industry. The more data you have access to, the easier it is to make correct decisions. A good warehouse management system will provide you with all of this data in an easily accessible form.
A WMS offers many opportunities to track and generate reports to oversee different aspects of your warehouse operations, such as pricing, tax systems, landed cost management, best-performing sales channels, peak sales season, most efficient picker, etc.
Inventory tracking & control
A modern, integrated WMS will let you track inventory movement at all times. Giving you a live inventory tracker. This is the first step in giving you control over your inventory. You can learn more about inventory control in this guide.
Cloud-based
It’s increasingly important you are not tied to your desk to access the information you need. Cloud-based systems allow you to access your WMS from anywhere you need.
Demand forecasting
Demand forecasting and the appropriate purchase order generation is a standard feature many leading WMS’s offer, which is important so that you don’t end up processing surplus orders. Veeqo comes with a powerful reporting and forecasting feature.
Learn More About Veeqo’s Warehouse Management Software
Key benefits of a WMS
Faster, more accurate fulfillment
Today’s ecommerce world requires being able to offer fast, reliable, delivery. Your customers will expect Amazon-like performance. If you can deliver it, you will get positive reviews and repeat customers. If you can’t meet this expectation, you will receive poor reviews and fewer repeat customers.
Whether you are a smaller ecommerce business or a larger operation, human error can still hold you back. Simple mistakes can result in mispicks, returns, and bad reviews. A WMS will drastically reduce the scope for human error. Both speeding up your fulfillment process and making it more accurate.
Connects your warehouse to your entire ecommerce operations
To succeed in the modern ecommerce world, you will need to make sure your sales channels and marketplaces are in sync with your warehouse process and inventory management. This way you can fulfil your customer orders accurately without having to worry about overselling, mispicks and returns.
Fulfil more orders with a smaller team
As a business grows and makes more sales, it can lead to their warehouse team growing in size. However, doing this leads to a more expensive and often less efficient warehouse operation. That’s one way a warehouse management system can prove its worth, by streamlining processes so that you can do more with a smaller team.
Manage multiple warehouses or just one location
As your ecommerce business grows, you may likely need more than one location from your stock. A warehouse management system will tie all of these locations together, giving you one source of data for each location.
More visibility
Warehouse management software should be able to provide everyone with the visibility they need to do their job accurately. This could include having a live dashboard everyone can see, providing an audit trail for all stock or live inventory counts.
The importance of digital picking
While many companies still do paper picking, more and more are turning to digital picking each year. Veeqo supports both paper and digital picking.
How digital picking works
Digital picking works by connecting the products you sell to those in your warehouse through a system of barcode scanning and batch picking.
Once a sale is made, an order is added to a queue to be picked by your warehouse team. A queue is simply a group of orders sent to your warehouse to be picked and shipped.
Once the picker accepts the batch, they then pick and scan the orders and take them to packing stations to be shipped.
Advantages of digital picking
The number of retailers taking advantage of digital picking is growing year on year. It’s a growing trend because:
It’s better for the environment
Digital picking saves paper with every order, helping reduce the carbon footprint of your business and the ecommerce industry as a whole.
It’s efficient and accurate
Digital picking reduces human error and optimizes the picking, packing and shipping process.
It’s flexible
Veeqo’s digital picking process allows the ability to override automation when it suits you, such as prioritizing certain orders.
To take advantage of digital picking in Veeqo you can either use the Veeqo App or the Veeqo Scanner.
The advantages of automation
As we’ve said above, automation is key to successful warehouse management. With Veeqo, the key benefits of automation are:
Automate warehouse tasks for increased efficiency
With Veeqo, you can create workflows to automate mundane tasks using custom triggers or conditions.
This lets you select shipping services based on delivery options, assign specific branded invoices to orders based on sales channel, add order tags based on customer ZIP code, and much more.
Update processes without decreasing accuracy
Changing processes as your business grows can be challenging, especially when your frontline teams need to adjust their operations.
With Veeqo’s automation, you can easily make changes to business logic, such as shipping services or priorities, without sacrificing accuracy or disrupting how the warehouse team works.
Use advanced picking batch creation to optimise your picking processes
One of the key ways you can reduce the scope for human error is by having your warehouse management system filter your orders into picking batches. These picking batches will figure out the optimal route for your pickers to take. Saving them time while picking and meaning your warehouse manager has one fewer job.
Save time with optimised picking routes
As businesses grow and their warehouse operations get more complex, it becomes more important to make sure the order pickers pick products is optimal. While not doing so may only cost minutes, these minutes quickly add up to real losses over time.
You tell Veeqo’s software the location of the different bins holding your products, Veeqo’s state-of-the-art software then works out the optimal route for your pickers to take.
Split picking lists between multiple pickers
Creating picking lists is a tedious process if you are trying to do it manually. You would need to figure out exactly the best items for each picker to pick based on order priority, bin location and more. Just to fulfill your orders.
A warehouse management system will manage all of this for you, so all your pickers have to do is press a button. You can learn more about digital picking with Veeqo in the below video.
In summary…
Warehouse management is a monumentally complex task with a wide variety of plates to keep spinning. But getting it right can be the difference between retail success or failure.
It all comes down to:
Arranging your layout properly and then organising your inventory within this.
Having a well-drilled system in place for staff to repeat time and time again when it comes to receiving stock and fulfilling orders.
Measuring efficiency, then identifying and fixing problem areas.
And knowing when it’s time to invest in a digital Warehouse Management System.
Get these aspects right and you’ll soon be running your warehouse like clockwork – and fulfilling customer orders quicker and more accurately than ever before.