Warehouse
How to Build a Warehouse for your Growing Business
- Written by Jana Gentry Smith
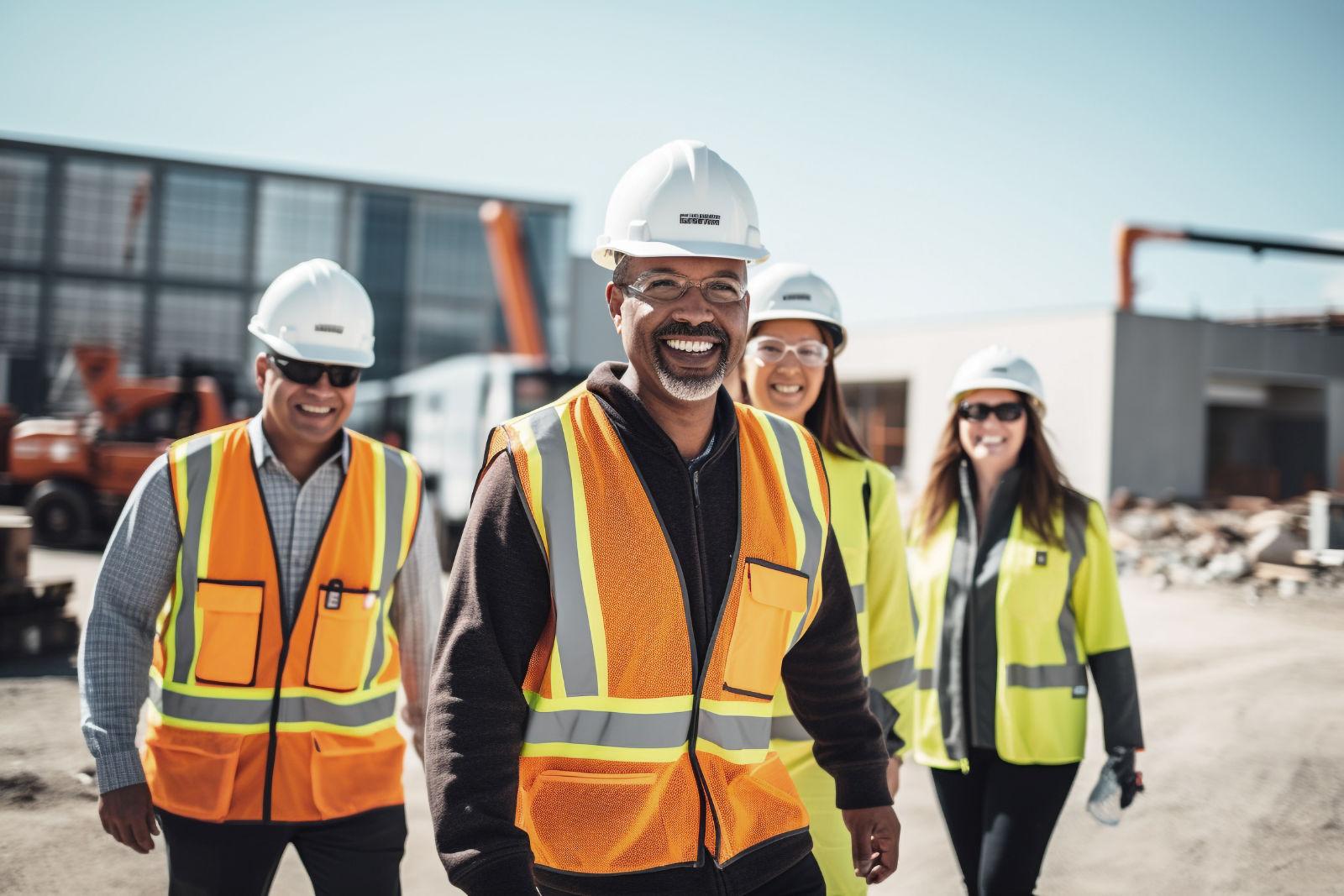
As your ecommerce business scales, you're confronted with the beginnings of a logistical nightmare. The time and money it’s taking to fulfill orders is adding up.
You might have inventory stored all over the place: garages, storage units, multiple smaller warehouses, and even your living room! It's time to invest in a larger warehouse to store all your inventory in one place, and while renting or buying can be a great solution, there are benefits to actually building your own warehouse for your growing enterprise.
It’s daunting, though, because there's that nagging fear of costly blunders and unforeseen hiccups. After all, the efficiency and functionality of your warehouse will be the linchpin of your entire operation, and surely it's easier just to rent or buy one that's already built?
Perhaps.
But there are benefits too. And if you do want to build and run an efficient warehouse, how do you do it without crashing and burning?
Keep reading for insights into where to build your warehouse, how to learn about zoning requirements, what to budget for, and how to find the right warehouse construction company.
Table of Contents
Choosing the Ideal Warehouse Location
Planning the Size and Layout of Your Warehouse
Navigate Zoning and Regulations
Set Your Warehouse Budget
Streamline Warehouse Operations
Safeguard Your Warehouse Assets
Prepare Your Warehouse for Growth
Enhance Warehouse Efficiency
10 Considerations for Choosing the Ideal Warehouse Location
When building a warehouse for your ecommerce business, choosing the right site is paramount. Here are ten key factors to consider:
1. Proximity to key transportation hubs
Choose to build your warehouse where it will be most efficient for shipping and receiving. Being close to major highways, ports, and customer distribution centers results in improved delivery times.
The right location saves you money on fuel and labor and keeps your customers happy because they receive their orders sooner.
On the flip side, prime locations can be expensive, and competition for space may be fierce, driving up land prices.
2. Cost of land
Balancing the cost of land and operational expenses with your budget is essential.
While opting for a lower-cost location might seem appealing, you might sacrifice proximity to customers or essential transportation infrastructure.
3. Safety and Scalability
Safety is a concern for every business, and choosing locations with a lower risk of theft and damage is a smart move.
When considering the long term, a location that allows for expansion without frequent relocations is valuable. But, these locations might have a steeper initial investment or are located in areas with lower customer density.
4. Market access
Consider the access to suppliers and markets.
After all, choosing a location near suppliers cuts the time required for restocking inventory, which helps meet customer demand. Being near your suppliers doesn’t guarantee you’ll be near your customers.
5. Environmental considerations
Thinking green often results in long-term savings. Implementing sustainable practices might require more money upfront, but the savings and reputation boost can be significant.
6. Tax incentives
Some areas offer tax incentives to attract businesses. Those savings free up your budget for other warehouse construction costs.
Keep in mind that relying solely on tax incentives may not be a sustainable strategy.
7. Labor availability
There are labor shortages all over, so much so that nearly 75% of supply chain executives are increasing their technology investments.
By choosing a location where there is a large enough labor pool to fill your warehouse positions, you’ll be able to attract people with a diverse set of skills.
Planning your warehouse layout is like playing a game of Tetris—it's all about strategically maximizing space to ensure smooth operations. Now that you’re location is pinned down, let's dive into the nitty-gritty of designing a layout that's as efficient as it is adaptable.
Plan the Size and Layout of Your Warehouse
When designing your ecommerce warehouse, the size and layout are pivotal factors that impact the efficiency and success of your shipping.
Here’s how to make informed decisions regarding your warehouse size and layout:
Determine the ideal warehouse size
When choosing your warehouse size, it can be tempting to plan only for what you need right now because the price tag for something larger feels steep. But planning for growth sets you up for longer-term savings because you won’t need to build an addition or relocate.
To make an informed decision, consider your answers to these questions:
What are your current and projected inventory volumes? Take into account growth projections, seasonal fluctuations, and products.
What are your operational needs? This includes order fulfillment processes, storage methods, and any specialized requirements.
What type of storage systems and material handling equipment will you use? This influences the spatial requirements and layout design.
How much space will you need for non-storage areas? Your warehouse will need offices, break rooms, and maintenance areas.
If you’re unsure how to answer any of these, consider consulting with warehouse design professionals for insights to help create a tailored solution that balances current and future needs.
Design an efficient layout for optimal operations
Since you’re starting fresh, you can design a warehouse layout that sets you up for efficiency well into the future. The layout impacts day-to-day productivity, safety, and performance. Consider the following aspects when planning your layout:
Safe and easy access to various areas within your warehouse will keep employees safe, help you stay legally compliant, and streamline your operations.
Sustainability and energy efficiency reduce environmental impact, lower operational costs, enhance your corporate image, and can lead to potential government incentives.
The right systems need to be in place to enjoy the benefits of efficient warehouse design. With that in mind, designing your warehouse involves careful planning, an effective inventory management system, and up-to-date technology.
Many warehouses are designed with a grid layout and divided into zones for receiving, storage, picking, and packing and shipping to maximize efficiency and provide employees with plenty of space for a safe working environment.
Inefficient layouts, on the other hand, often lead to operational bottlenecks by increasing labor costs and delaying order fulfillment.
Navigate Zoning and Regulations
Local zoning regulations play a role in shaping a community and ensuring that businesses operate in harmony with their surroundings. Complying with these regulations shows that your business is a responsible and considerate neighbor.
Keep in mind that compliance is a legal requirement. Non-compliance leads to legal consequences that include fines, legal disputes, and forced closures.
Since you plan to comply with zoning regulations, note these limitations and how they can impact your warehouse project:
Location: Regulations determining where warehouses can be located within a jurisdiction can impact your access to transportation networks, suppliers, and customers.
Land use: Zoning regulations dictating how to use land may restrict activities or require specific land-use designations.
Building size: Regulations often limit the size and height of buildings and can affect the capacity and layout of your warehouse.
Operational hours: Zoning regulations may restrict your warehouse’s operation hours, which might affect satisfying customer demand.
Environmental impact: Zoning regulations may set requirements for mitigating environmental effects.
These local rules might seem like bureaucratic red tape, but they are pivotal in shaping how and where businesses can operate. Here’s where to find information about your warehouse locations’ zoning regulations:
5 Resources for learning about your warehouse’s zoning regulations
Here are crucial steps to help you understand and adhere to these regulations:
Check local government websites for guides and documents related to zoning codes.
Consult local zoning officials or planning commissions for personalized guidance and answers.
Hire a zoning attorney who understands zoning laws and can expedite the process.
Attend local public zoning meetings to learn about upcoming zoning changes and regulations.
Check local codes and ordinances that outline zoning regulations and restrictions.
To set up your warehouse smoothly and in compliance with regulations, you need to fully grasp zoning rules. This involves accessing official resources, seeking expert advice, and staying updated on local changes.
Set your warehouse build budget
Constructing a warehouse isn't like buying a flat-pack bookcase. Costs vary wildly depending on the size, materials, and quality of the build.
That's why you should collect quotes, talk to a few suppliers, and dig into the details before you set your budget in stone.
Here are some considerations to research before spending a dime:
Construction costs: Get multiple quotes from experts based on size, materials, and location.
Permits: Determine the specific permits—and associated costs—required by local authorities.
Utilities: Contact providers for connection fees, monthly charges, and infrastructure upgrades.
Budget buffer: Allocate 10-20% of the budget for unexpected expenses or overruns.
Ongoing operational expenses: Estimate costs for labor, insurance, taxes, maintenance, security, and equipment.
Also, pay attention to the supplies, technology, and software you'll need inside the warehouse when you start crunching numbers. When designing your warehouse, think about the equipment you'll need, such as:
Bins
Totes
Printers
Picking carts
Shelving units
Packing desks
Shipping scales
Shipping computers
Packaging materials
Closed-circuit television (CCTV for security)
Your equipment selections should match your warehouse requirements and operations. Consider both the space they require and their impact on your budget.
And of course, you can save thousands each year by using a free all-in-one software solution like Veeqo, that can help with shipping, inventory, and warehouse management, rather than using an alternative that charges you per shipment amount or just for connecting your own carrier rates.
Streamline warehouse operations with technology and automation
Choosing the right level of technology—like wifi, computers, and printers— and automation is one of the keys to your ecommerce business’s success.
While more automation improves organization and customer satisfaction, it can come with high initial costs and technical challenges during integration.
Select the Warehouse Management System that suits your ecommerce warehouse
A Warehouse Management System (WMS) is like a super-smart helper for your warehouse. It does several things to make your warehouse work better.
Manages inventory efficiently: Keep an eye on stock so you know what's there and where it is.
Reduces fulfillment times: Handle orders from start to finish so they're accurate and sent quickly.
Boosts worker satisfaction: Employees work faster with fewer mistakes using barcode scanners.
Know how your warehouse is doing: Smart reports enable better safety stock management.
When you choose a warehouse management system—like Veeqo—consider your needs, like how big your business is, what you want to improve, and how much you want to spend.
A good WMS can help organize your warehouse so it works better and helps your business grow. The high upfront costs can be a potential drawback, but the long-term efficiency gains often outweigh these initial expenses.
Safeguard your warehouse assets
As your e-commerce business grows, you'll face new challenges, especially when keeping things safe. Your warehouse should do more than just protect from weather like fire and rain—it should also guard against theft.
Preventing theft
Securing your inventory calls for a multifaceted approach that includes physical, electronic, and procedural security measures:
Access control: Key card systems or biometric authentication limit entry.
Surveillance: CCTV cameras monitor, deter, and serve as evidence.
Alarms: Security alarms detect intruders and swiftly notify of a breach.
Lighting: Adequate exterior and interior lighting discourages unauthorized access.
Inventory management systems: Advanced systems to track and record inventory movements.
Physical barriers: Locks, security grills, and barriers on doors and windows add security.
Of course, you want to keep your goods safe and sound. But remember, your most valuable assets walk out the door every evening to their friends and families—your employees.
Let's shift gears to the human element of safety. How can we create an environment that not only keeps your inventory secure but also keeps your employees safe and injury-free?
Prioritize worker safety
We're not just talking about slapping a "Safety First" sign on the wall.
A well-designed space plays a huge role in worker safety. Think wide aisles to avoid collisions, clear signage to direct traffic, and enough room for everyone to do their jobs without elbowing their neighbor.
Plus, meeting Occupational Health and Safety Administration (OSHA) standards isn't just a box to check off. It's our ticket to a safer, happier, and more productive work environment. It's a win-win-win, really. Here’s why:
Fewer accidents and injuries promote well-being and morale.
A safer and more productive environment reduces absenteeism and curbs turnover rates.
Compliance with safety regulations helps you avoid legal troubles, fines, and reputational damage.
A positive work atmosphere boosts teamwork, operational efficiency, and profitability.
Neglecting safety measures results in a host of issues, like accidents, employee turnover, legal problems, and delayed operations.
Prioritize sustainability in your warehouse design
Sustainability isn't just a buzzword in warehouse design; it’s a game-changer for a few reasons:
Environmental responsibility: Sustainable warehouses reduce their ecological footprint, helping protect the planet for future generations.
Operational cost savings: Sustainable features like energy-efficient lighting, insulation, and renewable energy sources can lower long-term operating costs.
Brand image enhancement: Eco-friendly practices improve your brand's image, attracting environmentally conscious customers and investors.
Being sustainable can cost more at the start. Still, it's worth it because it saves money later and makes your brand look awesome. It's a smart choice for the planet, your wallet, and your reputation.
Choose Reliable Construction and Supply Partners
In the warehouse world, selecting experienced and reliable construction partners is a must. Here's why it's so important and how it can help you steer clear of problems:
Benefits of experienced partners | Drawbacks of inadequate partners |
Quality assurance Timely completion Cost efficiency Regulatory compliance Risk protection | Quality issues Budget overruns Legal problems Reputation damage Operational delays Security Risks |
Since the warehousing and storage services market size is expected to increase from $692 billion in 2023 to $974 billion by 2028, you can expect construction companies to be busy. That’s why you shouldn’t delay thorough vetting of construction companies. Here’s what to look for:
Assess their experience and track record in warehouse construction.
View their portfolios of similar projects.
Check for relevant licenses, certifications, and insurance.
Seek references and feedback from past clients.
Evaluate their ability to adhere to timelines and budgets.
Ensure they are well-versed in regulatory compliance.
Before you decide, think about if they match your project's goals, budget, and how you like to communicate.
Finding the company that fits your needs helps ensure your warehouse is completed efficiently, cost-effectively, and to the highest standards.
Prepare Your Warehouse for Your Ecommerce Company’s Growth
As your e-commerce business expands, your warehouse should seamlessly accommodate this growth. Here's why it matters:
Efficient inventory management
A well-designed, scalable warehouse and quality inventory management software make your inventory easier to pick for orders, so you spend less on shipping and make customers happy.
Digital picking
Using digital picking, such as with Veeqo's free mobile app or with the Veeqo Scanner, improves efficiencies and reduces things like misspicks.
The Veeqo Scanner is a stand-alone wireless device designed to improve and speed up the order picking process by helping your team pick faster and more accurately. It's the same scanner used in Amazon fulfilment centers, so you can be sure that you're warehouse will be able to maximise efficiencies to that coveted Amazon-level.
Reduced touchpoints
Having fewer steps in the supply chain means you spend less and have less chance of things getting damaged.
If you organize your warehouse and how you do things well, it means you handle your products less and move them better, which keeps your money and your products safe, too.
Cost-effective expansion
As your company grows, adaptable storage and infrastructure make it easy to expand your warehouse without spending much money on moving or building significant additions.
Even though preparing for growth costs money upfront, it saves you more in the long run. Your warehouse becomes a helpful tool for your e-commerce business and improves as it grows.
Enhance Warehouse Efficiency with Veeqo
Building a warehouse that suits your growing business is a big deal. While it may require a hefty initial investment, the long-term benefits are worth it.
What’s more, a warehouse built with growth in mind is a hidden gem–it saves you money, streamlines operations, and paves the way for business expansion.
Planning and running a new warehouse can be a bit of a puzzle, but tools like Veeqo make it easier. Veeqo's shipping, inventory, and warehouse management software streamlines your warehouse, reduces errors, and keeps customers happy.
Are you ready to build a warehouse that’s a well-oiled machine? When you’re ready to implement the future of shipping and warehouse management software, sign-up to Veeqo - it's free to use, and being owned by Amazon means it integrates seamlessly with Buy Shipping and AtoZ protection.